Automated Pickling Line Also Performs Pressure Testing
written: 29.05.2024Automated Product Handling and Inspection
We developed an automatic conveyor system for a heat technology manufacturer, enabling both pickling and pressure testing of products. The system integrates roller conveyors, chain-roller transitions, modular belt conveyors, and a transfer cart with dual roller conveyors, forming a comprehensive line for pickling and testing.
Products are loaded onto the input conveyors using a manual cart. Atypically shaped products are placed in special plastic trays equipped with RFID identification chips to ensure correct orientation on the line. A pneumatic stopper on the manual cart and the entrance structure also verify proper insertion, making the operation easy, convenient, and fully automated, without requiring manual intervention.
Fourfold Security Measures for Safety
At the entrance, a muting gate with variously oriented light barriers distinguishes between products and humans, stopping the line if an unauthorized object is detected. Once loaded, products are automatically grouped into sets of 4, 8, or 12 for easy handling by the pickling line manipulator. From the midpoint onward, the conveyors are made of chemically resistant stainless steel and placed in a plastic tray, ensuring an efficient pickling process while protecting the products, line, and hall environment.
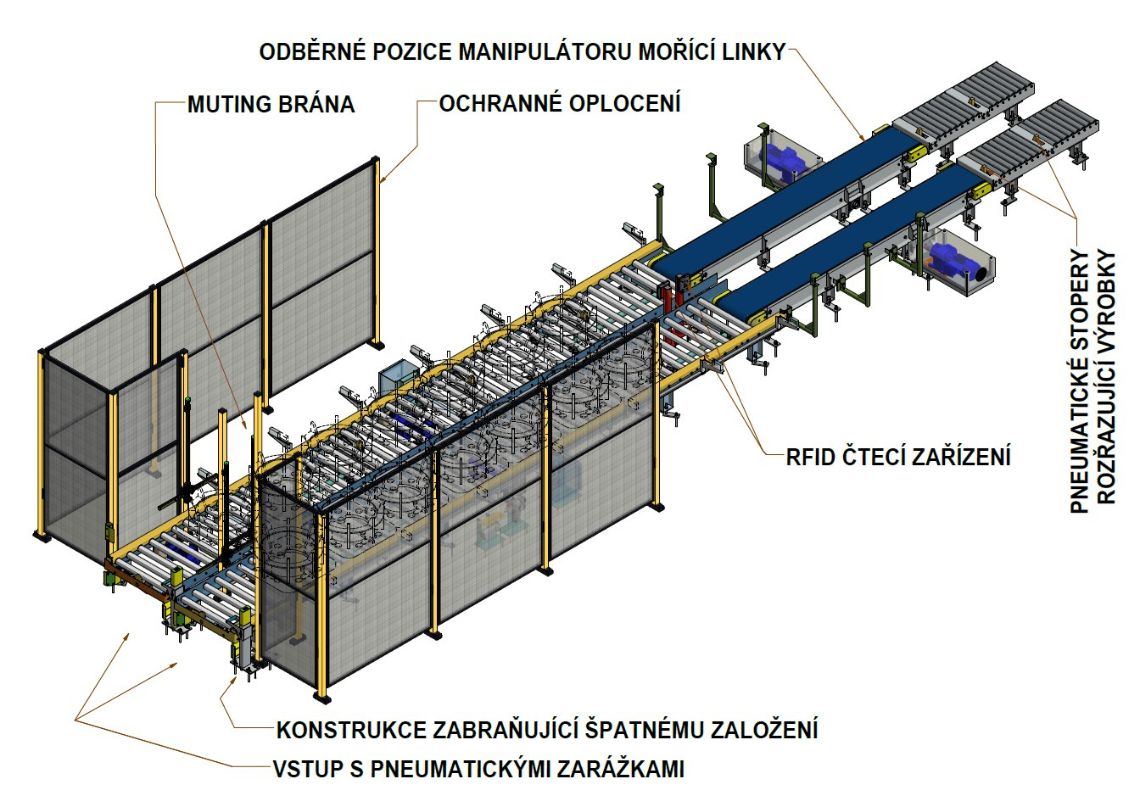
Integrated Testing Devices
At the output of the pickling line, a manipulator places products onto a stainless steel conveyor with a modular belt. Products move to roller conveyors, where they are sorted and redirected using a chain-roller transition. Parallel conveyors merge into one track, lining up the products sequentially. Along the conveyor line, six devices perform pressure tests on the products. Midway through, products stop, and the transfer cart moves them to available testing devices.
Automatic Separation and Retesting of Defective Products
The transfer cart continuously brings products for testing or returns tested ones to the roller conveyor. Products are sorted into OK or NOK categories, sending successfully tested products to one output and failed ones to another. Repaired products do not require re-pickling, so the output from the pickling line includes an entry for repaired items.
Operators load repaired products using a manual cart, and the system assigns them for further testing. For safety, all entries and exits are equipped with muting gates, stopping the line whenever a worker enters the automation area.
Interested in our solutions? Explore more examples of our work:
- Learn how our new repackaging line excelled in the demanding pharmaceutical industry conditions. Instead of a three-person crew, only one operator is now needed.
- Our sorting line, which automatically handles everything from letters to large packages, doubled the capacity of a transshipment point. Packages move at speeds over 13 km/h and overcome a height difference of 7 meters, allowing the logistics center to process up to 100,000 packages per shift.
- For another client, we replaced an overhead track with a line featuring lifting bridges, freeing up significant space in the hall and accelerating material flow.
Contact us to discuss how we can streamline your company's operations.